
Evan Erculiani's Portfolio
Personal Projects
Mini Bike Project
I started off by purchasing an old run down mini bike that did not run with the intentions of upgrading the engine. Over the course of the project I installed a 212cc predator engine, created a custom exhaust manifold, modified frame components, upgraded the engines air and fuel system, installed a torque converter transmission, and fabricated a disc brake system.
(Scroll)
Autocross Project Car
My love for cars has always been strong so when I turned 16 I saved up for a Mazda RX-8. At the time of purchase I wasn't aware that I had invested in one of the most educational processes of my life. Through my obsession for this car I learned a lot about working with my hands, fabrication, budgeting, and racing. After many years of modifying this vehicle I installed all of the modifications below in my garage with my own two hands.
-
Cold air intake
-
Catback exhaust system
-
Mid pipe modifications
-
Coil over suspension
-
Strut tower reinforcement
-
Lighting modifications
-
ECU accesport integration
-
Rolled fenders
-
Miscellaneous body modifications
-
Splitter rod fabrication
-
Racing tires and wheels
-
All maintenance
(Scroll)
New Standard Corporation
Floyd Kitting
During my time at New Standard Corporation I worked very closely with the R&D process, manufacturing process, and packaging process of the Floyd headboard, table, and bed kits.
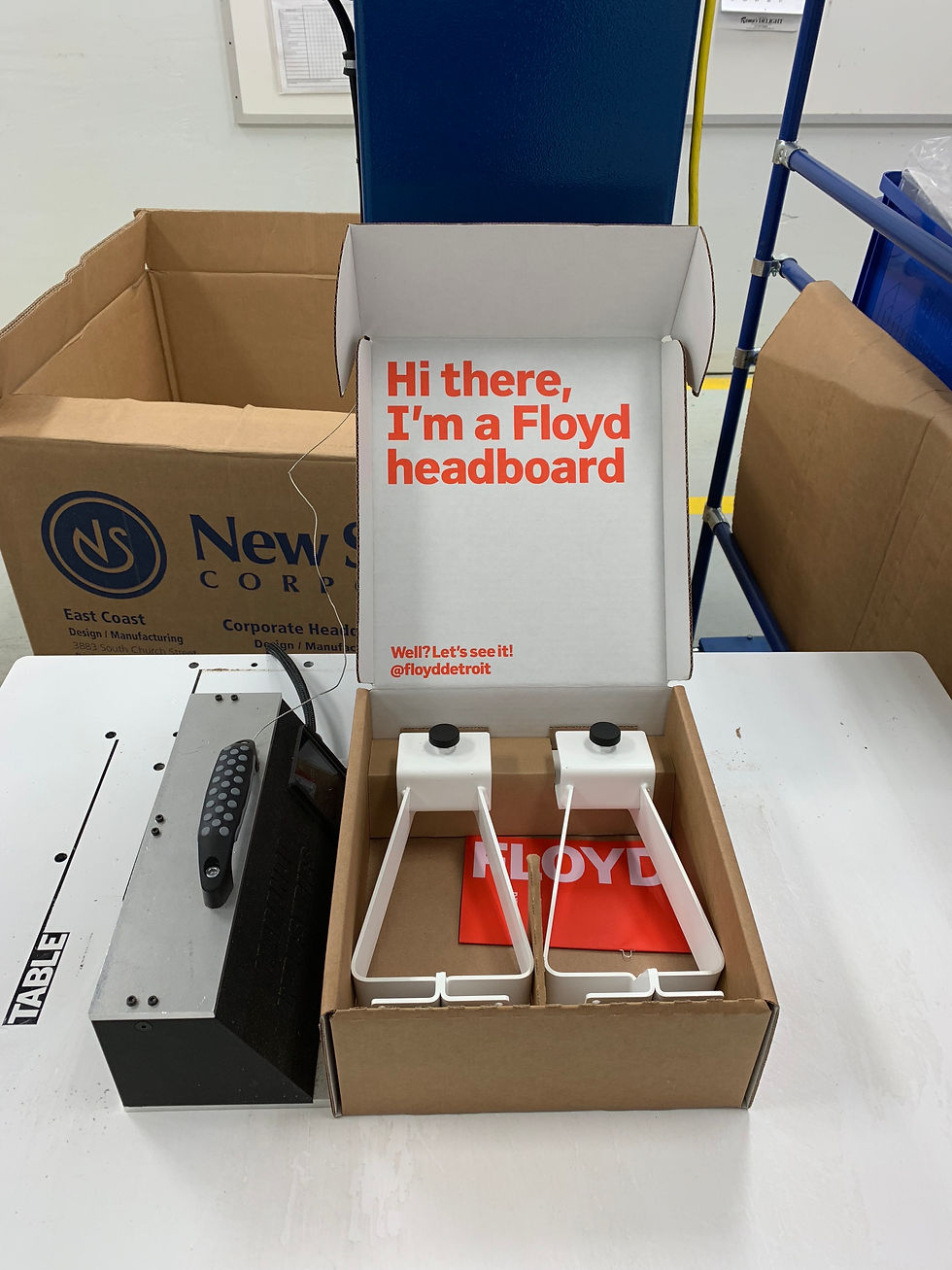






Gilbarco Gas Pumps
During the project of integrating a new line of gas pumps into the Gilbarco line I was able to closely observe the R&D Process. I also created a fixture gage for a bracket on the gas pump used to verify critical dimensions on the part. Once all of the manufacturing wrinkles were ironed out and first production pieces were manufactured I then became heavily involved in process changeover from the E700 model to the E900 model.
Formula SAE Project
Coming into the project I was awarded frame team lead and was later voted onto a three person, decision making committee. Our goal for this years frame was to shorten the overall length by 5in, achieve a torsional rigidity of 1200ft*lb/deg, keep the frame as light as possible and deliver a final product that was almost identical to the SolidWorks model. Throughout three semesters, 21 frame revisions, and months of fabrication we produced a frame that met each and every one of our design goals while still accommodating to all of the FSAE rules. This was the single most educational and rewarding projects that I have ever been a part of and resulted in a final product that our team and I were extremely proud of.
(Scroll)
Attention: Some projects are not photographed or discussed due to the companies confidentiality policies
Stay In Touch.
